'The employer just didn't do their own thorough investigation about what actually happened'
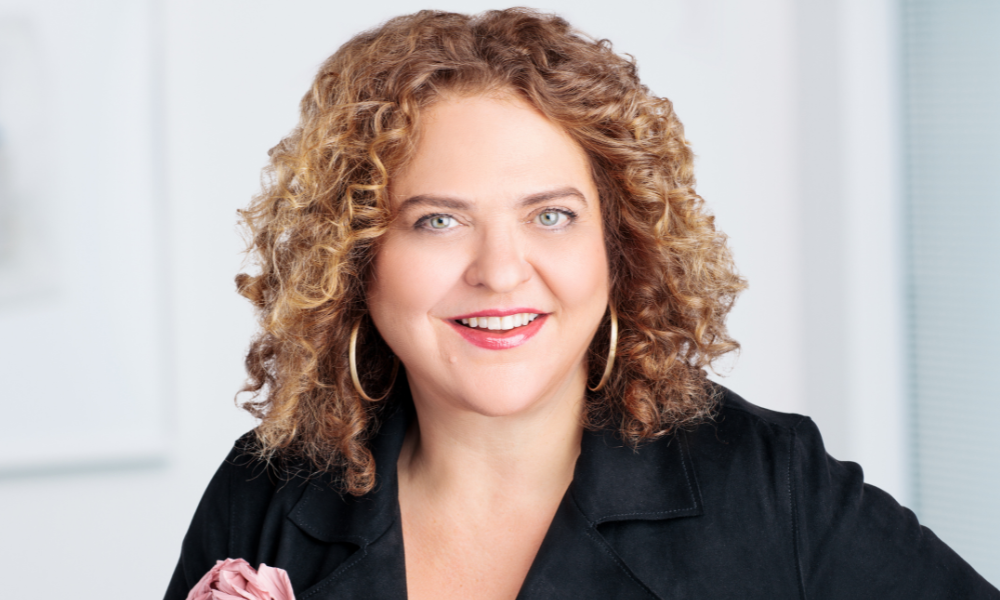
Termination of employment was excessive for a British Columbia worker who committed a serious safety infraction but was apologetic and had no previous safety violations, an arbitrator has ruled.